About Beryl
By 2030: 1 mln tons plastic waste will be turned into aromatics and 300.000 tons plastic waste will be turned into wax
What is Beryl?
A new technology...
“The Beryl-Process” will build on, and strengthen proven pyrolysis technology. It will effectively purify and transform mixed plastic waste into new high value waxes and aromatics that can be transported back to the chemical and petrochemical industry for reprocessing into products without using fossil raw material: a true circular process.
Experience...
Two experts from the petrochemical industry, together with an experienced entrepreneur in durable and sustainable solutions have incorporated this new technology venture; Beryl Circular B.V. in The Netherlands, focusing on the recycling of mixed plastics waste and converting them into virgin chemical building blocks; waxes and aromatics.
The Beryl-Process...
Is the next step combined with conventional pyrolysis to create a circular and low-emission CO2 process: by effectively converting a broad range of plastic waste into raw materials for the plastics industry at near zero CO2-emissions.
Chemical recycling...
Is technology that is able to deal with a broad spectrum and varying mixed, contaminated and layered waste plastics, which nowadays is collected and supplied through all waste collection and sorting plants in the world. It is important to cooperate with both key partners in the supply chain from plastic waste to the virgin final product, as well as with technology providers in chemical processing and catalysis.
Beryl Circular ...
Cooperates with both key partners in the supply chain from plastic waste to final virgin product, as well as with technology providers in chemical processing and catalysis.
From conventional waste plastic...
In conventional waste collecting programs only a small part of plastic waste is separated, collected and mechanically or chemically recycled including pyrolysis, but most plastic waste is still landfilled or incinerated. Oil refining is needed to convert fossil fuel into new plastics.
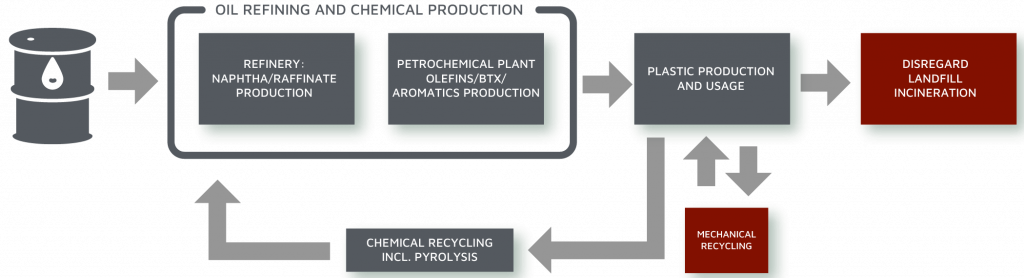
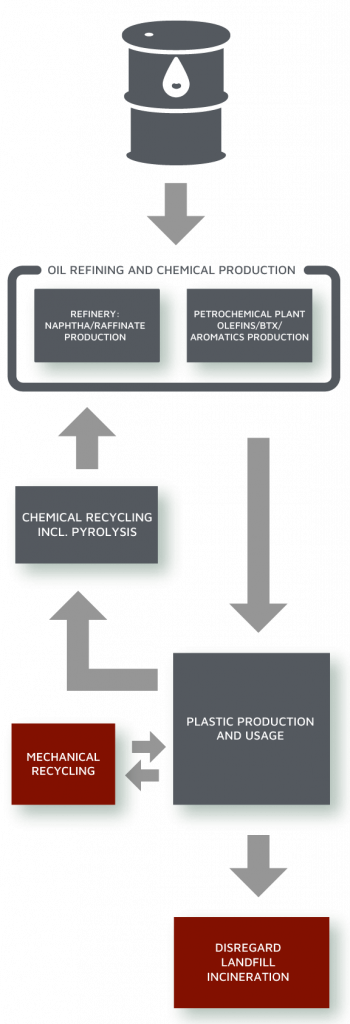
To the Beryl Process
The Beryl Process takes mixed waste plastics as feed and produces waxes and aromatics. In pyrolysis thermal energy (heat) disrupts the plastic polymers into wax, diesel, naphtha and LPG. In the proprietary Beryl process, a catalyst converts the into waxes and aromatics (and removes contaminants such as chlorine and bromine from the hydrocarbon products). The waxes are both slack waxes and micro crystalline waxes. The aromatics: benzene, toluene and xylenes. These products can be easily stored and readily transported to a site for blending or further rectification, depending on the final application, such as use of raw materials into new plastics.
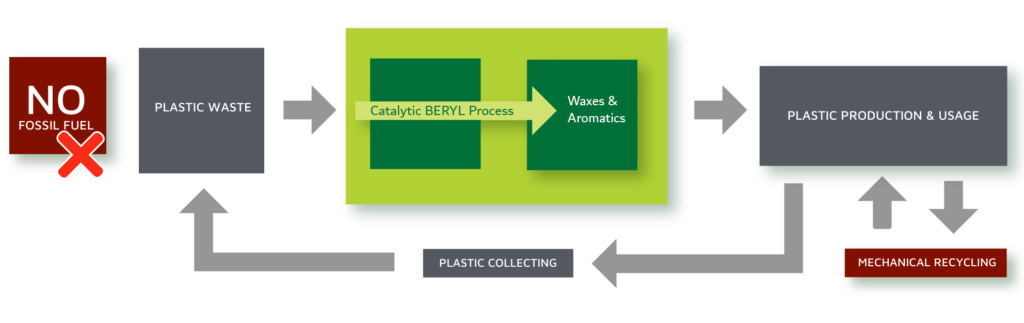
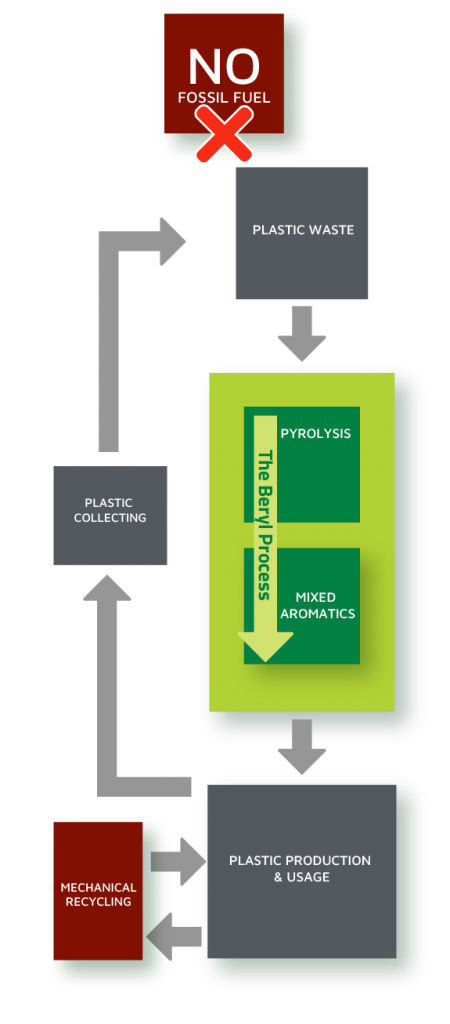
“Today there is no other commercially operated catalytic process capable of doing so.” This process leads to:
Growth funding for converting waste plastics into high-quality waxes
, We have secured growth funding from GMP Group and the Energy Transition Fund Rotterdam to scale up our innovative technology, which converts waste plastics into high-quality waxes. We are also happy that we received a grant from the Just Transition Fund, this implicates that Beryl is Co-financed by the European Union. In this next phase, we will set up a pilot installation at PlantOne Rotterdam to scale up our new B-Wax technology.
Beryl’s mission is to convert 25,000 tons per annum of waste plastics into 20,000 tons of high-quality waxes in the first large scale production site. The new B-Wax technology can process a wide range of plastic waste, delivered through existing plastic waste collecting and sorting facilities in Europe. After completing the pilot program in 2025, construction of a commercial B-Wax factory is planned for 2027/2028 in Rotterdam.The use of waste plastics underlines the circularity of the B-Wax process, excluding the use of oil. Additionally, European buyers of waxes are realizing, due to both short term and long term geopolitical changes, that they need to source their waxes more locally.
The B-Wax technology is scalable and self-sustaining in energy. Excess thermal energy generated during the process is converted and made available for resale to third parties as electricity and for district heating networks.