Get informed
Read up about recycling & circular plastics
people, Planet, Profit
The Beryl process contributes to a cleaner environment by reducing waste plastics and reducing carbon and nitrogen emissions
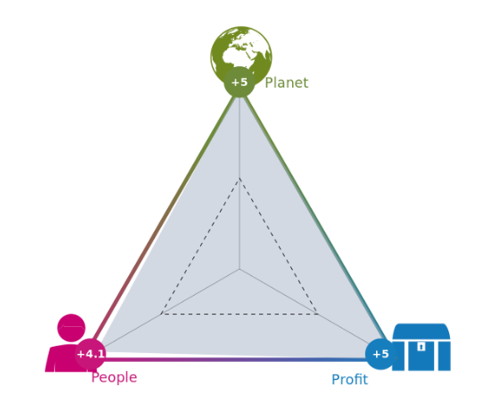
By gearing up a new process Beryl helps to transition from a carbon intensive economy to a green economy. People with valuable skills currently working in the petrochemical industry can use their skills to create novel and clean processes in companies actively contributing to sustainable solutions. Beryl wants to help the next generations not just by realizing a cleaner environment but also by becoming a training center of excellence for employees and students who are eager to develop skills to create a new green future.
plastic Lifecycle
The plastics lifecycle, including 1950-2015 cumulative plastic production and waste generation
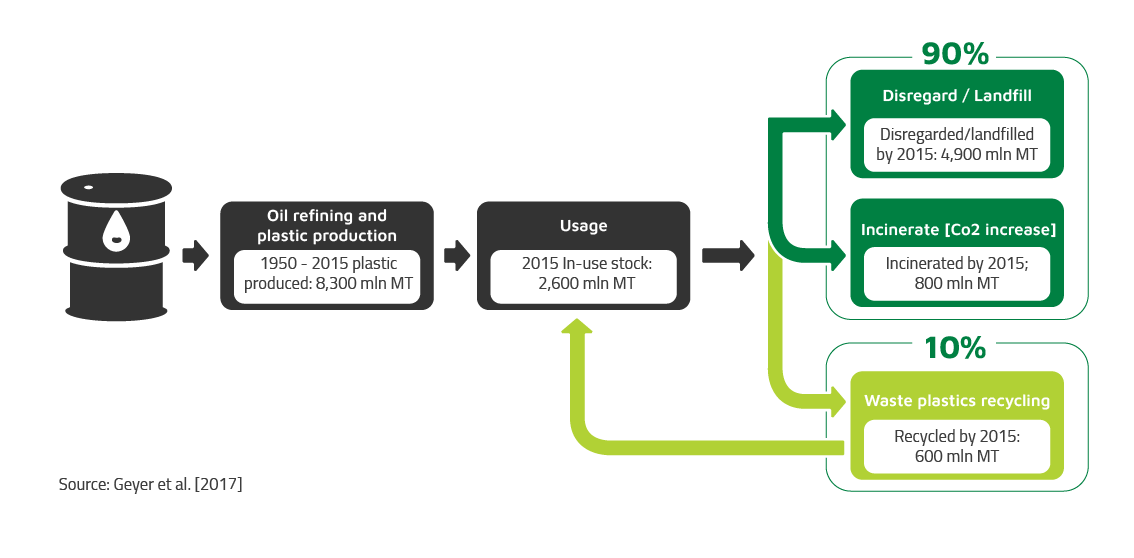
Of all plastics ever produced about 2.6 billion tons is currently in use. Between 1950 and 2015 the cumulative waste generation amounted to about 6.3 billion tons, of which only 600 million tons (10%) have been recycled. 5,700 million tons (90%) have been disregarded and landfilled or incinerated. Research into the environmental impacts of waste plastics has accelerated in recent years, showing all sorts of negative outcomes on both humans and animals of not properly recycling plastic waste.
Europe today
The European Union has already adopted strict legislation such as complete landfill bans, extended producer responsibility and specific recycling targets. In January 2018, the European Commission announced a vision for Europe’s new plastics economy, as part of the new set of measures announced within the 2018 Circular Economy Package.
The evolution of landfilling
Collection, recycling, incineration and landfilling rates are distributed unevenly across Europe. In countries where landfill bans are in effect (Belgium, Luxembourg, Netherlands, Germany, Denmark, Switzerland, Austria, Norway and Sweden), less than 10% of plastic waste is landfilled. In other countries, such as Spain and Greece, a staggering amount of over 50% of all plastic waste still finds its way to landfill. Landfilling rates
The European Strategy for plastics outlines the following commitments to be implemented:
all plastic packaging used in the European market is to be cost-competitively reused or recycled by 2030;
more than half of plastic waste generated in Europe must be recycled;
plastic sorting and recycling capacity must be expanded four-fold by 2030, relative to 2015 levels;
Realising commitments resulting in 200 000 new jobs;
10 million tons of recycled plastic is to be used for new products by 2025.
Recycling methods
Mechanical recycling
Plastics can be recovered from plastic waste via mechanical recycling. Here plastics are recovered via mechanical processes (i.e. grinding, washing, separating, drying, re-granulating and compounding). In mechanical recycling the polymers stay intact, this permits for multiple re-use of polymers in the same or similar product — effectively creating a closed loop.
However, these plastics need to be strictly sorted on plastic type (and even on colour), washed very thoroughly. Still, in the end the plastic polymers do suffer during the use and recycling and therefore the amount of recycled plastics that can be used in products is limited.
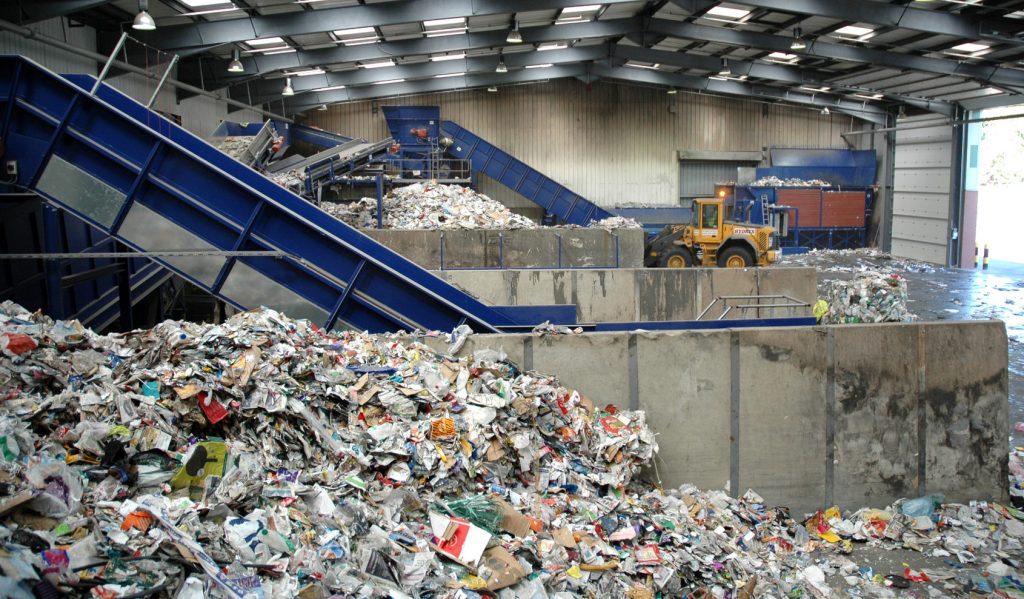
“Operators strive to separate and clean the different plastic types. However, there is a growing stream of plastics and plastics-containing waste (rejects) that cannot be sustainably mechanically recycled to the required standard from an economic and environmental perspective. This waste plastic stream provides a valuable resource for other recovery solutions such as chemical recycling.”
For some plastic waste streams it is impossible, or economically not feasible, to sort them properly for mechanical recycling.
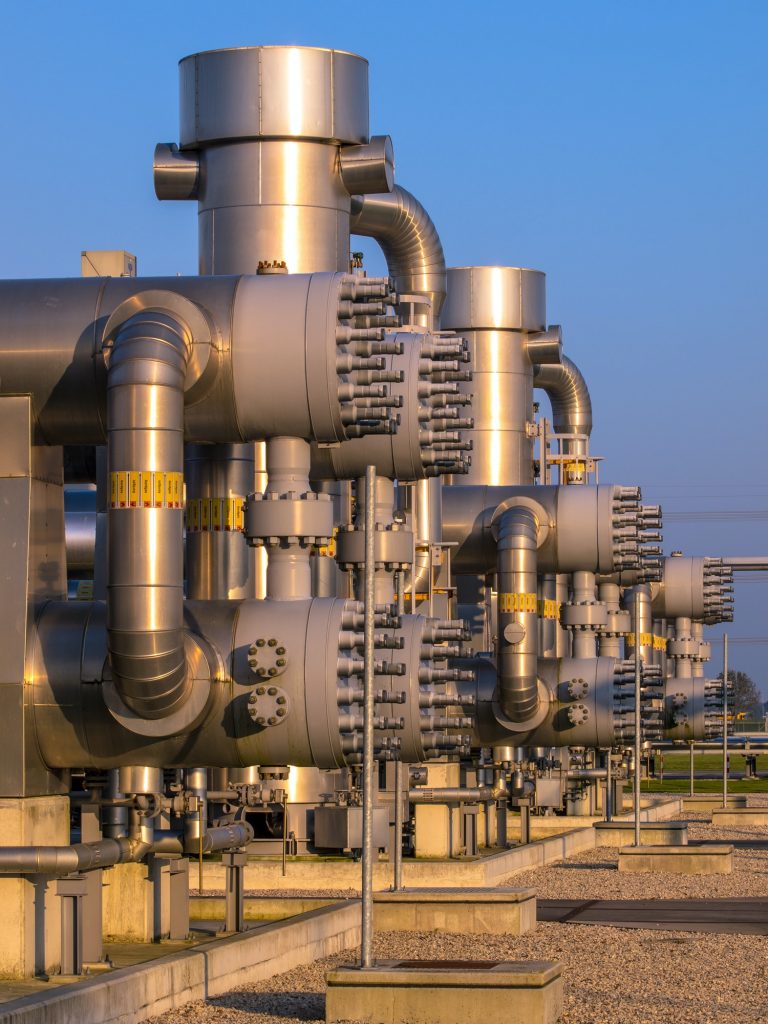
Chemical Recycling
Where plastic waste cannot be perfectly separated, chemical recycling can convert plastics into a myriad of products: fuels, naphtha as feedstock for petrochemical plants, monomers to make new plastics and building blocks for new materials. These materials are now made from plastic waste, and not from fossil fuels directly. Frequently the production of fuels is excluded from the definition of chemical recycling, as fuels are a product that directly produce CO2 when used.
Where in mechanical recycling the plastic polymers do not change, the purpose of chemical recycling is to break the long polymers down into smaller products that can be used directly (fuels) or are building blocks for new materials (waxes and aromatics for example) or monomers to synthesize new polymers.
The main technology used in chemical recycling is thermal cracking in the absence of oxygen: pyrolysis. In this process, the polymer chains are broken by thermal energy, bringing them back into the original monomers or a mix of these together with other cracking products. The products from the thermal cracking process are diesel products and depending on the severity of the operation. The presence of contaminants such as chlorine hampers the introduction of many pyrolysis concepts that did not address the cleaning up of the hydrocarbon waste stream
The Beryl Process
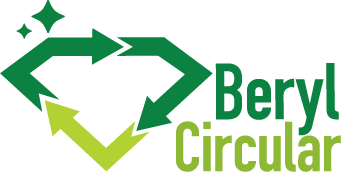
When using the Beryl Process, contaminants will be dealt with and a much higher value output is realized. The output of the Beryl Process is rich in waxes or aromatics. Waxes and aromatics can be used as raw materials for the production of a wide variety products, while eliminating the use of fossil fuel and reducing the carbon footprint in a substantial way.
Aromatics (BTX)
Aromatics as building blocks for the plastics industry are Benzene, Toluene, and Xylenes (BTX). Most of these aromatic hydrocarbons are initially produced as a mixture via catalytic reforming of naphtha in a petroleum refinery plant or via steam cracking in a petrochemical plant.
Benzene is a commodity petrochemical product. Aromatics are liquid products and easily can be stored and transported.
Aromatics can be used as fuel additive as octane booster, in paints & coatings, cleaning agent, foams and as the chemical solvent or chemical intermediate in the manufacture of plastics, surfactant, rubber, adhesives, detergent, lubricants and medical drugs.
Europe's chemical industry is a world leader in chemical production. More than half of the chemical sales in the region (EU-27) are of polymers and petrochemicals, which in turn propels the demand for BTX.
More information is available at:
WAX
Waxes are linear hydrocarbon molecules with 20 to 60 carbon atoms. Waxes come in various qualities, from slack wax (low melting point and high oil content) to micro crystalline waxes (high melting point and low oil content). These waxes are incorporated into consumer or industrial products to make them water repellent, sealable, more flexible, or easier to process.
Slack waxes are used in many applications such as coatings and lubricants where micro crystalline waxes are used in high end applications such as cosmetics, pharma, additives to polymers and food.
The market for wax in 2021 was $9.8 billion and is expected to grow to $ 12 billion in 2027 (CAGR 4.3%). The non-fossil technology, thus reducing CO2 emissions, has already received enthusiastic responses from potential wax buyers
. Beryl has developed a novel process to convert waste plastics into industrial waxes on bench scale. By utilizing waste plastics to replace fossil fuels for the production of industrial wax allows in chemical recycling closes the loop in the plastic life cycle.
CO2 and other emissions
Decarbonization of the economy and transition to a sustainable society has substantial effect on energy intensive industries using oil and gas, the people employed by these industries and the regions where these industries operate. The petrochemical industry is a prime example of this.
The petrochemical industry is among the most carbon intensive industries. Clean alternatives such as the process developed by Beryl will reduce the carbon intensity and reduce CO2 emissions. Beryl will convert 15 kta waste plastics in the first commercial plant. The alternative for this plastic waste is incineration in a municipal solid waste plant. Compared to incineration, the Beryl process reduces CO2 emissions by 26 kta.
The process utilizes waste plastics that would otherwise be incinerated, dumped, or broken down into microplastics in the environment. The reduction in incineration of plastics reduces the emissions of nitrogen and nitrogen oxides. Air and water qualities will improve, as most of the environment will, by avoiding the incineration of waste plastics and creating a useful product at the same time.).